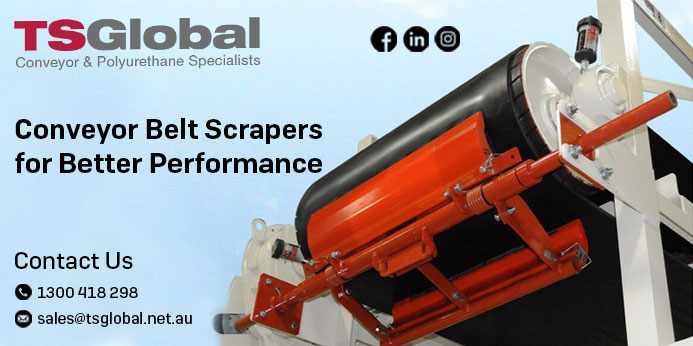
Conveyor systems play a vital role in numerous industries, facilitating the efficient movement of materials across production lines, warehouses, and processing facilities. Despite their importance, conveyor systems often face challenges that can lead to inefficiencies, wear, and unexpected downtime. One critical factor influencing conveyor performance is belt traction, which directly impacts productivity and longevity. Pulley lagging is an essential solution that enhances belt traction, optimizes performance, and prolongs the lifespan of both the pulley and conveyor belt.
Understanding Pulley Lagging
Pulley lagging & Conveyor Belt refers to the process of covering the surface of conveyor pulleys with a material that increases friction and reduces slippage between the pulley and the conveyor belt. This added layer of material improves traction, ensuring smoother operation and better alignment of the belt.
Pulley lagging can be made from a variety of materials, including rubber, ceramic, and polyurethane. Each material type offers specific benefits suited to different operational environments. The selection of the appropriate lagging material is crucial for maximizing efficiency and minimizing wear and tear.
Why Belt Traction Matters
Belt traction is a key element in conveyor systems, influencing how efficiently the belt carries materials. Poor traction can lead to belt slippage, misalignment, and uneven material flow, resulting in reduced throughput and increased maintenance costs. Traction issues may also cause excessive wear on the belt and pulley, shortening their lifespan.
Enhanced traction provides several benefits, such as:
· Reduced Slippage: Lagging increases friction, preventing the belt from slipping, especially in high-torque or heavy-load conditions.
· Improved Belt Alignment: Better traction ensures the belt remains aligned, reducing the risk of side drift and spillage.
· Increased Lifespan: By minimizing slippage and reducing wear, lagging helps extend the life of the pulley and belt.
· Higher Efficiency: With improved traction, the conveyor can operate at higher speeds and handle heavier loads without compromising performance.
Types of Pulley Lagging
Choosing the right type of pulley lagging depends on the specific needs of the operation. Here are the most common types:
1. Rubber Lagging: Rubber is the most widely used material for pulley lagging. It offers excellent friction, durability, and resistance to abrasion. Rubber lagging is suitable for general-purpose conveyor systems and is often used in mining, aggregate, and manufacturing industries.
2. Ceramic Lagging: Ceramic lagging is ideal for heavy-duty applications requiring maximum traction and wear resistance. Embedded ceramic tiles provide superior grip and are effective in wet or high-torque environments. This type of lagging is commonly used in mining, bulk material handling, and other extreme conditions.
3. Polyurethane Lagging: Polyurethane lagging offers excellent abrasion resistance and flexibility. It is lightweight, making it an ideal choice for applications where reducing overall system weight is essential. Polyurethane lagging is often used in food processing and pharmaceutical industries.
4. Strip Lagging: Strip lagging involves applying strips of lagging material to the pulley rather than covering the entire surface. This method provides cost-effective traction enhancement and is useful in applications with lower load requirements.
5. Weld-On Lagging: Weld-on lagging involves directly welding steel or ceramic tiles onto the pulley surface. This provides extreme durability and is suitable for high-impact applications.
Key Considerations for Pulley Lagging Installation
Installing pulley lagging requires careful planning and execution to ensure optimal results. Here are some important factors to consider:
· Material Selection: Choose the lagging material based on the operational environment, load requirements, and conveyor type.
· Pulley Condition: Ensure the pulley surface is clean, free of debris, and in good condition before applying lagging.
· Lagging Thickness: The thickness of the lagging material should be appropriate for the application. Thicker lagging offers more durability but may add additional weight.
· Temperature Resistance: Consider the operating temperature and select lagging that can withstand extreme conditions.
· Installation Method: Proper bonding techniques, such as cold bonding or vulcanization, must be used to secure the lagging firmly to the pulley.
Benefits of Regular Lagging Maintenance
Regular maintenance of pulley lagging & Conveyor Belt Scraper is essential for maintaining conveyor efficiency. Over time, lagging can wear out, reducing its effectiveness. Periodic inspections and timely replacements help prevent costly downtime and ensure continuous productivity.
Key maintenance practices include:
· Routine Inspections: Regularly check for signs of wear, cracking, or peeling of the lagging material.
· Cleaning: Keep the pulley and lagging clean to prevent material buildup that can affect traction.
· Monitoring Performance: Observe conveyor performance and address any slippage or alignment issues promptly.
· Timely Replacement: Replace lagging when signs of significant wear appear, ensuring the system continues to operate smoothly.
Industry Applications
Pulley lagging is used across various industries to enhance conveyor efficiency and reliability. Some of the key industries include:
· Mining: In mining operations, pulley lagging helps manage the heavy loads and abrasive materials commonly encountered.
· Agriculture: Conveyor systems in agriculture benefit from lagging by reducing material spillage and ensuring smooth transport of grains and produce.
· Manufacturing: In manufacturing facilities, pulley lagging enhances production line efficiency by preventing belt slippage and ensuring consistent material flow.
· Logistics and Warehousing: Lagging improves the performance of conveyor belts used in warehouses and distribution centers, ensuring seamless operations.
Conclusion
Enhancing belt traction through pulley lagging is a cost-effective way to improve the performance and longevity of conveyor systems. By selecting the right type of lagging and maintaining it regularly, businesses can minimize downtime, increase productivity, and extend the life of their conveyor components. Investing in quality pulley lagging ultimately leads to smoother operations and greater operational efficiency, making it a crucial aspect of conveyor system maintenance and optimization.
Write a comment ...